Case Study: Shift handover communication as an element of digital transformation
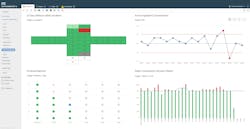
Orion Engineered Carbons produces carbon black, which is a solid form of carbon used for tires, coatings, ink, batteries, plastics and other high-performance applications in the automotive and technology industries. The company has 14 production sites and four technical centers. Orion chose its Ivanhoe, Louisiana, plant to implement a solution for enhanced communication — providing the highest quality product while maintaining a single repository of information for all team members.
Located deep in the Louisiana bayou, Orion’s Ivanhoe plant has been running continuously since 1952. The daily challenge the 40-person team at Ivanhoe faces is keeping this vital cog in the industrial supply chain running at full production, 24x7. Ivanhoe production manager, Zach Kristicevich, who oversees plant operations, was instrumental in onboarding the eschbach Shiftconnector platform throughout the facility.
Communication for plant effectiveness
The company chose Shiftconnector to provide team communication between shift teams to better ensure safety and improve plant effectiveness. Shift handovers are simplified by tracking and managing essential information in a single digital repository. This knowledge capture means each shift can see what happened during the prior shift as well as having access to historical data for continuous improvement.
Orion’s Ivanhoe facility contains a formidable array of chemical and mechanical manufacturing technologies, including high-temperature furnace reactors, pulverizing systems, granulators, dryers and bagger/packaging systems. Orion’s tank farm stores bunker oil, the primary raw material for the plant. Connected via pipeline to the Gulf of Mexico (about a mile away), the plant is replenished every two weeks with feedstock from a tanker. The presence of so much combustible material at the site underlines the importance of safety and the need for operators to follow inspection protocols rigorously.
The company makes every effort to promote safety to make sure that employees feel that processes are safe, so vigilance and accountability are critical for following inspection processes and checking regimens. Orion considers digital tools like Shiftconnector to be extremely helpful, reminding staff of safety rounds, for example. Also, having a real-time overview of production lets the company get a handle on a situation quickly before it becomes a safety problem.
Challenges within Orion’s manufacturing process
The Ivanhoe facility’s main production area, a roofless behemoth the size of a three-story building, contains the main reactors, which combine air, oil and natural gas at temperatures greater than 2000°C. This process of controlled combustion is used to form particles of carbon black in many different grades to meet customer needs. The carbon black is then formed into pellets and packaged for transportation.
The reactors are a critical aspect of production and keeping them producing at or near their capacity requires seamless communication between operations, engineering and maintenance.
To meet customer requirements for more durable tires, advanced films and coatings, as well as pigments, Orion needs to constantly fine-tune operating parameters. This means everyone needs to be on the same page, even those on the night shift. Before Shiftconnector, communicating — especially between different shift teams — was sometimes difficult or inconsistent. “Now with digital technology, the operation is transparent - everyone knows what is important, what work is ongoing and on-deck, and who has the ball. It gives the whole team more confidence,” Kristicevich said.
A particular challenge is Ivanhoe’s location in “hurricane country.” Over the past few years, the facility has had both direct and near-direct hits requiring plant shutdowns. But there is no quick off-switch for this operation. A strict protocol must be followed by all staff, and the shutdown procedure can take days. Having support for a digital handover of information between teams is essential. For example, reactors must be slowly cooled to avoid damaging their advanced ceramic linings. Losing just one reactor would drastically impact production. There are many other activities that need to be documented and tracked, and having one digital record for the different shifts to follow is essential to a safe and environmentally secure shutdown.
The plant control room is in the center of the unit. Protective gear must be used to muffle the loud whirring of blowers, compressors and other equipment. Air ducts wind through the unit like a roller coaster, conveying carbon black from one step in the process to the next. Inside the control room, there is a command post from which every production step is monitored. An array of monitors provides readings from critical machinery and applications.
The control room is always staffed, and Orion built a system where the operator can have input from operational technology as well as IT systems. Over time, however, applications multiplied. This created time constraints when operators needed to sign in to do their work. It also required a steep learning curve. Operators depended on paper records and email. According to Kristicevich, people just did not have time to search emails or spreadsheets or look for the right document. Shiftconnector brings a single system of record that has the most up-to-date condition of the operation. Maintenance requests can be entered directly into the company’s SAP system from Shiftconnector. Previously, people needed training to access SAP just to inform maintenance. Now operators can do this, and more, from their own Shiftconnector cockpit, saving time and alleviating stress.
The control room faces immense tail gas blowers pushing exhaust to the sulfur recovery and tail gas treatment systems. Environmental conditions are a top concern. According to Kristicevich, operators are all from the area and want to be eco-friendly, so sustainability is important to Orion. Scrubbers have been installed for the tail gas exhaust and teams make daily checks of equipment, via Shiftconnector, to minimize environmental impact.
Without measurement, there is no control. Environmental reports were previously done on paper and now they are online with Shiftconnector. The plant manager can monitor compliance with procedures, which was much more difficult and time-consuming on paper.
The packaging area is where the final product is shipped to market. The plant has its own rail line for bulk deliveries. Pure carbon black drops into each car from a product silo. Here are the beginnings of the tread for truck tires, a phone case and a laptop touch screen display. Each of the million or so particles has been engineered for the specific application, with nanometer precision.
Change management and operator acceptance
The Ivanhoe team has had a strong and positive reaction to Shiftconnector’s software. It is something that works specifically for the plant floor as it follows the way teams work and how they track processes. This is because Shiftconnector is set up specifically for the plant and is organized around team functions, on a shift-to-shift basis, keeping people informed and engaged.
While there was some expected resistance from long-time employees, after a short learning curve it has been completely embraced because of the time savings and communications transparency. For newer employees with less experience, it has provided a valuable knowledge base of processes and protocols to reinforce operational best practices. As Kristicevich says, “The accounting, sales and supply chain departments have had their own systems for a long time, but finally we have something to connect the shop-floor workers.”
Conclusion
Why does having digital tools for front-line staff in manufacturing matter? Because they leverage knowledge about the operations at its most critical juncture: the nexus of operational execution, quality, safety and compliance (environmental, social governance or otherwise).
Making use of granular data on the ground also helps with optimizing the overall operation and contributing to margins and the bottom line. Over the past 30 years, manufacturing has invested prodigiously in logistics to leverage the global supply chain. Digital tools serve to put data to good use with those who will find it most helpful. Thus, paying attention to information logistics — getting data into the hands of those that need it most — will certainly pay dividends.
Andreas Eschbach is the founder and CEO of the software company eschbach, which helps production teams stay safe and work smarter through better information sharing and collaboration. Holding a degree in computer science, he draws his practical experience from leading a variety of international software consulting and implementation projects for leading chemical manufacturing companies, focusing on production, continuous improvement, EHS and maintenance. His company is a provider of manufacturing solutions and headquartered in southern Germany and has an office in Boston, Massachusetts.
eschbach
Orion Engineered Carbons