Food-grade lubricants play critical role in food and beverage manufacturing
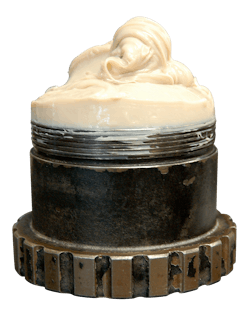
In the fast-paced world of food and beverage manufacturing, the importance of proper lubrication often goes unnoticed. However, the right lubricants play a crucial role in maintaining safety, efficiency and regulatory compliance. Food-grade lubricants, specifically designed for use in food processing and handling equipment, are essential components in preventing contamination and ensuring smooth operations.
Understanding food-grade lubricants
Food-grade lubricants are not edible substances like cooking oils or salad dressings. Instead, they are specially formulated lubricants safe for use in food processing equipment. These lubricants must meet strict safety standards, as they may potentially come into contact with food products during the manufacturing process.
The U.S. Food and Drug Administration has established guidelines for lubricants used in food processing and handling applications. According to these regulations, food is considered contaminated and must be discarded if it contains an amount of lubricant exceeding 10 parts per million.
Types of food-grade lubricants
Lubricants used in the food and beverage industry fall under two primary classifications.
1. NSF H1 lubricants: These are designed for the possibility of incidental food contact and are used in equipment where there is a possibility of the lubricant coming into contact with food products. NSF H1 lubricants must comply with FDA regulations and are approved by the National Sanitation Foundation.
2. USDA H2 lubricants: These are used in equipment that indirectly supports food and beverage processing and handling, such as forklifts. While not intended for the possibility of incidental food contact, they must still meet specific safety requirements.
The importance of food-grade lubricants
Food-grade lubricants are critical for several reasons:
1. Contamination prevention: They eliminate the risk of product contamination in case of leaks or incidental contact, safeguarding food integrity.
2. Regulatory compliance: Using appropriate food-grade lubricants helps manufacturers meet strict industry regulations and standards.
3. Cost savings: By preventing contamination, these lubricants can help avoid costly product recalls. According to NSF, more than half of all product recalls between 2008 and 2017 were due to biotoxins and chemical contamination, with a single recall potentially costing a manufacturer around $10 million.
4. Equipment protection: Food-grade lubricants are formulated to protect machinery from wear and tear, extending equipment life and reducing maintenance costs.
Choosing the right lubricant
Selecting the appropriate food-grade lubricant depends on the specific application and equipment. Factors to consider include:
- Risk of food contact
- Operating conditions (temperature, load, speed)
- Equipment type (conveyors, pumps, mixers, etc.)
- Compliance requirements (NSF H1, USDA H2, Kosher, Halal)
Food-grade lubricants are an essential component of safe and efficient food and beverage manufacturing. By understanding their importance and choosing the right products, manufacturers can protect their operations, comply with regulations and maintain the integrity of their products.