Getting it right on the packaging line with vacuum conveyors
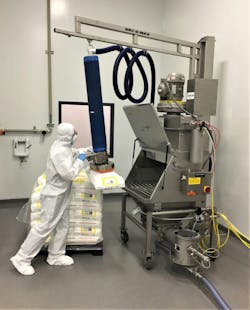
Manual handling methods and mechanical feeders may have once provided an economical solution for loading packaging equipment, but such methods can become stumbling blocks on packaging lines. Problems include inconsistent filling resulting in costly production interruptions; product loss through spillage, overfilling and product degradation; extended downtime to clean and maintain mechanical feeders; and an assortment of safety hazards.
To stay competitive, many processors are replacing outdated manual methods and faulty equipment in their packaging suites with vacuum conveyors, which deliver tangible improvements in uptime, efficiency, labor costs, safety, productivity and product quality.
Vacuum conveyor benefits and operation
Vacuum conveyors enable operators to safely load materials from floor level to up-and-over packaging equipment. Because these systems use suction to move material through tubular conveying lines, any leakage in the system is drawn inward. This prevents particulates that can endanger workers, jam expensive equipment or cause cross contamination from entering the environment. Vacuum conveying systems are also fully enclosed with no moving parts, protecting materials from air, dirt and waste.
Their small footprint, simple operation and flexibility make vacuum conveyors the dominant choice for product transfer to packaging machines. Vacuum conveyors easily integrate into just about any process operation because conveying lines can be routed between floors, through partitions and around machinery and can easily be rerouted when process modifications occur.
A vacuum conveying system consists of five basic components: a pickup point where material is introduced into the system, a vacuum producer that powers the system, a vacuum receiver (also called a filter receiver) that collects transferred material, convey tubing in which material is transferred and a control module that regulates conveying cycles and interfaces with other machinery.
Although vacuum conveying systems are relatively simple, they are not one-size-fits-all solutions. To ensure success when adding a system to a packaging line, it is critical to understand the characteristics of the material being conveyed and how those characteristics will interact with the equipment design.
Vacuum conveying is as much an art as it is a science. Expert manufacturers that have experience with thousands of applications can anticipate solutions in a broader framework rather than simply addressing a primary goal. Common user concerns such as downtime for sanitation and cleaning, machine utilization and worker safety have led to innovative designs such as column-lift and mobile systems that lower conveyors to floor height for faster and safer cleaning, changeover and maintenance.
Selecting vacuum conveying equipment
Processors wanting to invest in vacuum technology to load filling equipment may not be sure exactly what they need. Working with a seasoned expert in vacuum conveying technology is the best way to ensure proper equipment selection. Expert vacuum conveyor manufacturers perform pre-order testing with the customer’s material under the customer’s working conditions, and then perform post-order factory acceptance tests (FAT) on the new equipment before it leaves the plant, ensuring that equipment arriving at the user’s facility operates predictably.
Choosing vacuum conveying equipment based solely on the lowest upfront cost often ends up costing more in the long run or fails to deliver the overall cost savings more carefully selected equipment ensures.
The following examples of two tea applications illustrate the flawed one-size-fits-all approach and the problem with choosing equipment based on lower upfront costs.
Example 1. In the first application, a private-label manufacturer of whole-leaf tea products purchased an extension conveyor to reduce the number of workers needed to move mobile silos between production equipment and packaging machines. Rather than purchasing a vacuum conveyor from the manufacturer of its existing vacuum conveying system, the private labeler chose what appeared to be an equivalent system but with a lower upfront cost.
However, the new extension conveyor generated more fine particles in the company’s high-grade, whole-leaf tea products. The fine tea dust, up to 200 microns in size, was susceptible to static charge and clung to the inside of the cellophane packaging that wrapped around the boxes. This resulted in quality-control issues and increased costs due to rejected product, extended cleaning times, wasted production effort and retrofitting costs to eliminate the problem.
After unsuccessful attempts to remedy the problem with the vendor of the extension conveyor system, the private labeler contacted the manufacturer of its existing vacuum conveying system for a solution.
After FAT with the private labeler’s materials, the conveying system manufacturer shipped a pre-engineered system with several retrofitted filter separators to integrate with the extension system, maximizing the amount of tea dust carryover drawn away from the extension system.
Carryover is product (dust) that is separated from the airstream and collected in the filter separator vessel to prevent the material from reaching the vacuum pump. Typically, companies want to minimize carryover to preserve product, but the whole-leaf tea application called for maximizing carryover, which eliminated 70-80% of the fine dust from the product.
Example 2. In the other tea application, an herbal supplement producer blended and processed pharmacopeial-grade herbs into tea bags and wanted to eliminate manual dumping of 100-pound barrels into hoppers and the need to use forklifts to bring materials to a mezzanine level. Minimizing carryover to preserve expensive ingredients was an important consideration during pre-order material testing.
During testing, it was determined that the three-filter system initially specified for the application was capturing more product than desired, so the conveyor manufacturer designed a single-filter system and adjusted the flow rate to achieve the desired level of carryover.
With the new system, rather than using forklifts to bring barrels up to the mezzanine level and manually scooping materials into the hopper, operators use a vacuum wand at the floor level to pneumatically transfer materials from the barrels to the equipment.
Improved safety is a common objective when processors move from manual handling to automated handling with vacuum conveyors. The new system eliminated forklift traffic, which is a giant safety improvement since forklift accidents are responsible for approximately 87 workplace deaths each year.
Additional vacuum conveyor options
Cleaning and maintenance are safer, more efficient and more effective when performed at ground level. This is especially critical in industries where stringent FDA and USDA sanitary regulations lead to frequent extended downtime for cleaning.
Mobile and column-lift vacuum conveyors are complete conveying systems that raise and lower the vacuum receiver to load taller equipment and then bring the vacuum receiver back down to ground level for cleaning or sanitizing, eliminating the need for stair climbing and/or mezzanines.
Sanitary design is a specialized field, and expert conveyor manufacturers have worked with thousands of materials and have decades of experience building hygienic vacuum conveyor systems. These manufacturers understand the different requirements for food, pharmaceutical, nutraceutical and cosmetics applications and know how to provide processors with the most efficient sanitary powder and bulk solids transfer systems.
Mobile conveyor systems have high utilization rates because a single mobile conveyor can service multiple processes. When one type of packaging machine finishes a production run, that machine may be idle for a period of time, but a mobile conveyor can be quickly cleaned and moved to another room for use with another product and packaging machine.
To further streamline cleaning and sanitation, some processors have two sets of convey lines and/or two sets of filters so they can quickly switch out dirty components for clean ones and clean the dirty components while the next process runs. Processors that run different flavors or colors might have filters dedicated to certain ingredients (such as cherry or licorice, for example).
Seek expert guidance
Although turnkey vacuum conveyor packages may be suitable for limited packaging applications, such as conveying excipients, active ingredients or nutraceutical powders to capsule filling machines, typically some level of customization is needed to comprehensively improve efficiency with a vacuum conveyor.
Saving on initial cost often does not lead to overall savings with vacuum conveyors. To ensure long-term savings and lasting performance in packaging operations, work with a seasoned vacuum conveyor manufacturer to ensure that the equipment is optimized for the specific material and application.
Doan Pendleton is president of Vac-U-Max, located in Belleville, New Jersey. His professional experience includes more than 35 years in the dry bulk solids handling industry, in addition to experience focused on plant safety and OSHA compliance with Vac-U-Max industrial vacuum cleaners. Doan has strong application expertise in the food, pharmaceutical, plastics, chemical, and non-wovens industries. He holds a Bachelor of Science degree in Marketing and Management from Suffolk University. Since 1954, Vac-U-Max has designed and manufactured bulk material handling and industrial vacuum cleaning systems and solutions for advanced manufacturing.
Vac-U-Max