Rotary batch mixer slashes cycle times and overages at contract manufacturer
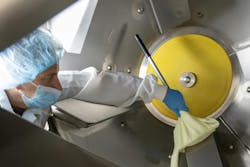
EW Packaging contract manufactures and packages powder, tablet and capsule products, protein powders, energy drink mixes, and sports nutrition products. Customers include national warehouse clubs and dietary supplement retailers.
Founded in 2001 as EW Trading dba EW Packaging, CEO Rob Lonas renamed the company EW Packaging when he brought the company’s packaging and printing services in house. Today EW operates six blister-filling lines and four bottle-filling lines and uses flexographic printers to customize pouch and blister foils. EW also machines its own tooling, which shortens turnaround times and reduces costs.
In 2016, the EW began blending dietary supplement and food powders and manufacturing tablets and capsules, but the company's V-cone blender proved inefficient. “The machine was a lot of work and there was a lot of downtime,” Lonas says. “It took at least 30 minutes to get a load in and out, plus another 15 to 20 minutes of actual mixing.”
Next, he tried a ribbon blender, which reduced loading and unloading times but compromised blend quality. “The ribbon blender has corners, dead zones, where the powder isn’t mixed,” he says. Sometimes EW added as much as 10 percent more active ingredient to the products than required for High-Performance Liquid Chromatography (HPLC) testing to confirm that the product met the label claim. In addition, the ribbon blender’s impeller put product quality at risk, Lonas says. “It chops up the ingredients and damages the product at the same time.”
Gentler, more accurate powder blending
To improve EW’s blending operation, Lonas purchased a 15-ft3 (425-liter) Munson rotary batch mixer that loads, blends, and discharges in about 15 minutes — half the time of the previous blenders. The unit’s horizontal vessel rotates on external trunnion rings located at each end, handling ingredients gently because it has no agitators. Instead, the vessel has internal flights that create a four-way tumble-turn-cut-fold mixing action, producing homogeneous blends without generating heat, shear or stratification. Lacking internal shafts, the mixer has no seals that are in contact with the product.
To initiate a blending cycle, operators hand-weigh ingredients into a drum. A plant-based protein product may contain up to eight ingredients, while a flavored creatine product may contain up to four. The drum containing the weighed batch is then lifted onto a mezzanine and dumped through a security screen into a hopper that discharges into the mixer’s stationary inlet. A collection hood contains fugitive dust during the loading process, while a single external seal prevents the escape of dust during vessel rotation.
Lonas highlights the rotary batch mixer’s gentle mixing action in his business conversations. “It's part of my sales pitch for whatever the job is — encapsulation, tableting or just blending a powder,” he says. “This mixer just folds in the ingredients. It’s not smashing them or pounding them together.”
Blends are discharged from the mixer through a stationary outlet. Batches destined for encapsulation or tableting flow into mobile hoppers that are rolled into the adjacent room for those processes. Powder products are discharged into a screw conveyor that transports the batch to the feed hopper of an auger filling machine, which dispenses the product by weight into bottles, canisters, tubs, or most any container.
The vessel leaves almost no residue following discharge. “There aren't any corners or pockets that can collect powder,” Lonas says. Between blending campaigns and when switching products, operators wash, rinse, and swab-test the vessel interior in accordance with Good Manufacturing Practices.
The blends are always on spec, and overages range between 2 percent and 3 percent instead of 10 percent as it was previously, says Lonas. “I sold my V-blender and my ribbon blender. The rotary batch mixer gives us a perfect HPLC test every time.”
A small blender with big output
Despite its modest volumetric capacity, the mixer outputs high volumes because it loads and discharges quickly and blend times are short, as little as 3 to 6 minutes, Lonas says. “When we started getting bigger orders, we got nervous at first thinking our mixer wasn't big enough, but we ran some big orders with no problems.” In one case, EW Packaging blended some 80 batches of a protein powder over four days, filling all of it into 5-lb (2.3-kg) tubs.
“The future for us is growing the powder business because we have our powder lines so dialed in,” Lonas says. “It’s a profitable and a fast way to fill bottles.” The company’s fastest line fills as many as 50,000 bottles per day, which includes capping, induction sealing, metal detecting, check-weighing, labeling, lot coding, and neck banding.
“We seldom tell customers ‘No’ unless they come in with a liquid,” Lonas says. “If we don’t have the right machinery, we buy it. Our niche is getting new products going for people and cranking them out, getting them into the market fast. We get a lot of business because of our blister capabilities and because we can do short-run stuff. There aren’t many other places on the West Coast that can do that.”
Lonas calls the rotary batch mixer his workhorse. “I think we changed a seal once. There's not much maintenance to do on it. It’s one our most reliable machines.”
Munson Machinery Co.
EW Packaging